The Inner Workings of DC Motors
A Comprehensive Guide on How They Work and Their Applications
Direct current (DC) motors, are the unsung heroes of electrical engineering and the driving force behind an extensive range of applications. In everything from household appliances, electric cars, and everything in between. Delving into the intricacies brings us on a journey into electromagnetism, mechanical motion, and the integration of components.
Fundamentals of DC Motors
At their core, DC motors convert electrical energy into mechanical motion. This transformation, rooted in the fundamental principles of electromagnetic induction, was first conceptualized by Michael Faraday in the 19th century. Understanding the mechanics of DC motors requires a grasp of magnetic fields and electric currents.
Components and Construction
The anatomy of a DC motor is an assembly of components working in unison. The armature, a pivotal component, is typically a coil of wire situated within the magnetic field created by the stationary stator. A commutator and brushes complete the trio, which facilitates the process of changing the direction of current in the armature coils as the motor rotates.
The armature is often wound with copper wire to enhance its magnetic properties, and the stator is designed to produce a magnetic field that interacts dynamically with the armature. The commutator, a rotary switch, ensures the continuous rotation of the armature by reversing the current direction at precise intervals.
How they Operate
The functionality of DC motors hinges on the generation of torque resulting from the interaction of magnetic fields. As a direct current flows through the armature coils, it produces a magnetic field. This magnetic field interacts with the magnetic field produced by the stator, creating a force—torque—that sets the armature in motion. The role of the commutator lies in orchestrating the timely reversal of current direction, which sustains the rotation.
Diverse Types of DC Motors
DC motors come in a variety of different types, each tailored to specific applications. Brushed DC motors, distinguished by the use of a commutator and brushes for current direction control, are common in household appliances and automotive systems. On the other hand, brushless DC motors(BLDC) leverage electronic controllers to achieve the same effect, making them more efficient and less prone to wear.
Beyond this, DC motors can be categorized based on their speed control methods. Series-wound motors, with the armature and field windings in series, are adept at providing high starting torque. Shunt-wound motors, with separate field windings, offer steady speed control. Compound-wound motors combine aspects of both series and shunt winding for a balance of torque and speed.
Everyday Applications
The ubiquity of DC motors in our daily lives is remarkable. From powering the rotation of ceiling fans and the vibrancy of electric toothbrushes to the intricate mechanisms within power tools, these motors are the silent champions of functionality and precision. In the industrial realm, they drive conveyor belts, pumps, and machinery, illustrating their versatility and reliability.
Conclusion
The exploration of DC motors transcends the technicalities of electrical engineering; it unveils a narrative of innovation, reliability, and progress. These motors, often hidden within the mechanisms of our daily conveniences, continue to shape our electrified world. Navigating their complex landscape offers not just technical insights but a profound appreciation for the subtle revolutions they bring to our lives.
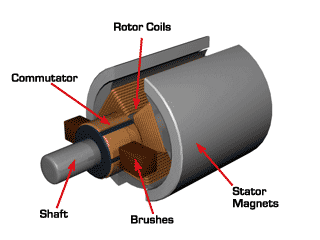
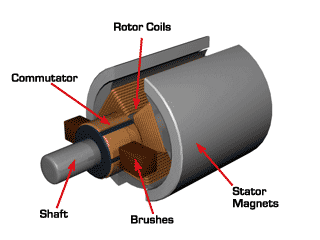
Image credit: electrical4u.com
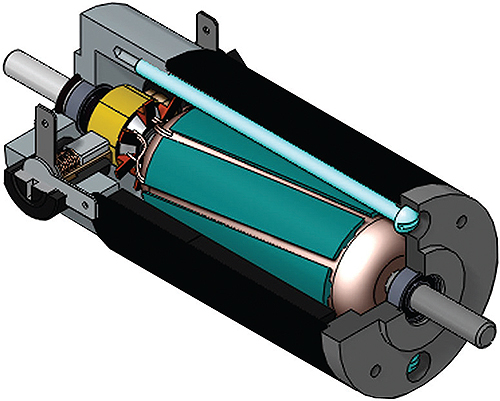
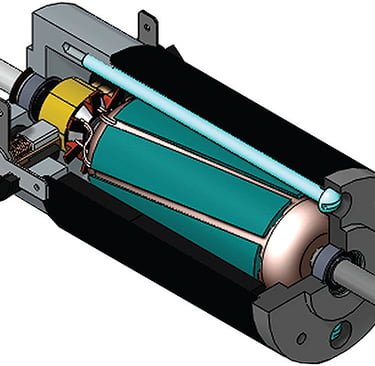
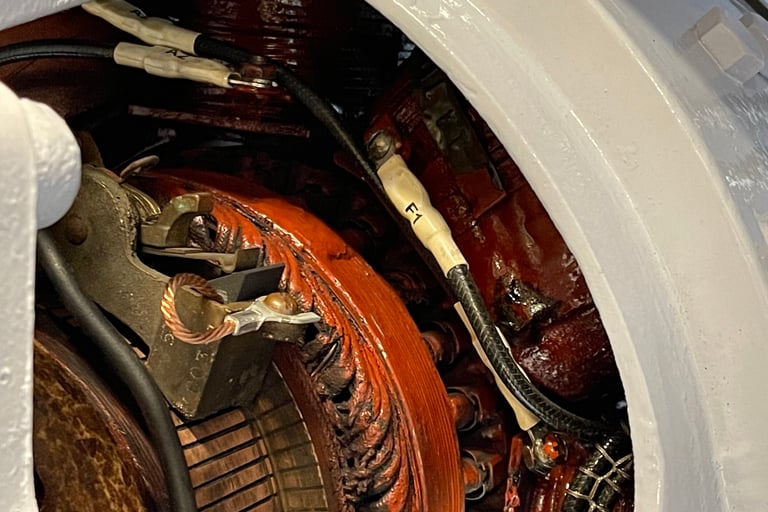
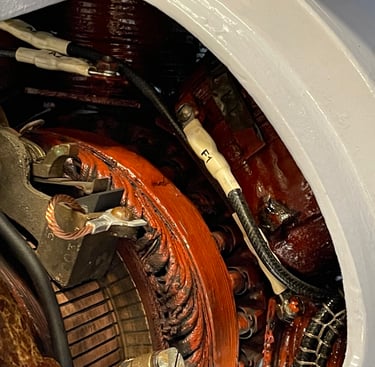
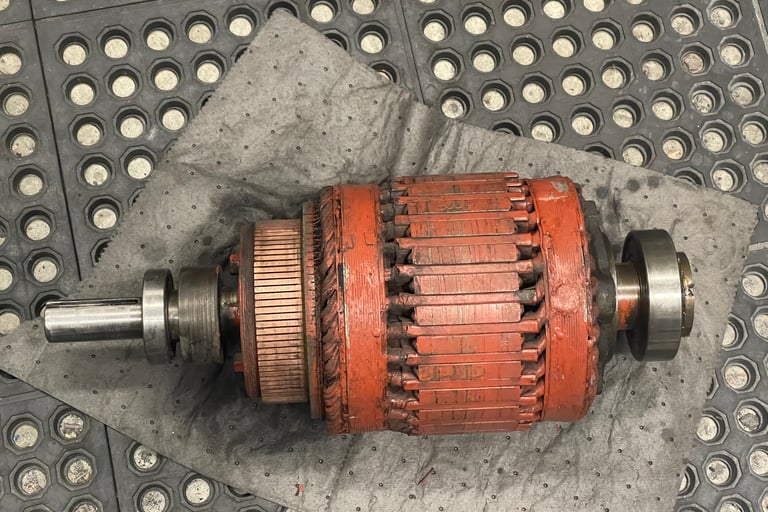
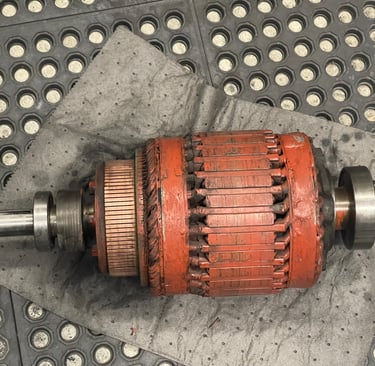